Carbon fiber, a material known for its exceptional strength, light weight, and versatility, has made significant inroads into various industries, particularly in the realm of industrial equipment. The use of carbon fiber tubes in machinery and industrial devices has revolutionized the design and functionality of these systems, offering numerous advantages over traditional materials such as steel and aluminum. In this blog, we’ll explore the diverse applications of carbon fiber tubes in industrial equipment and how they are driving innovation in this field.
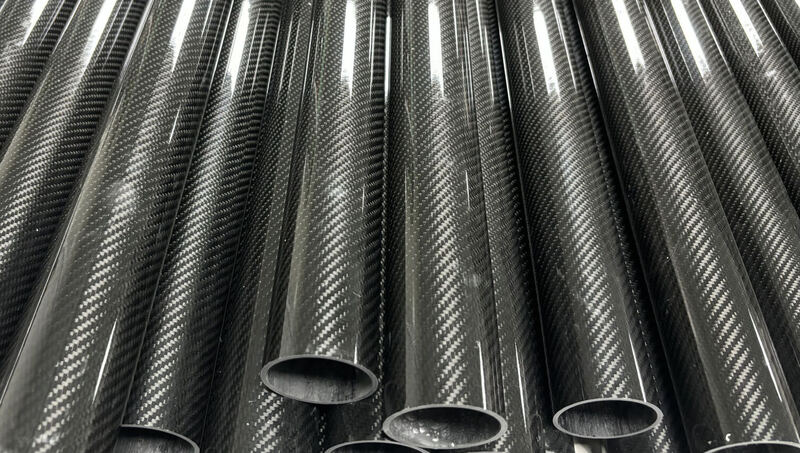
1. Superior Strength-to-Weight Ratio
One of the primary reasons carbon fiber tubes are favored in industrial equipment is their superior strength-to-weight ratio. Carbon fiber is five times stronger than steel yet weighs significantly less. This unique combination allows for the development of robust yet lightweight structures, which is particularly advantageous in applications where both strength and weight are critical factors.
A. Robotic Arms and Automation Equipment
In robotic arms and automation equipment, the use of carbon fiber tubes enhances both precision and speed. The lightweight nature of carbon fiber reduces the inertia of moving parts, allowing for faster and more accurate movements. This is crucial in high-speed manufacturing environments where precision and efficiency are paramount.
B. CNC Machining Components
CNC machines often require components that can withstand high forces without bending or warping. Carbon fiber tubes provide the rigidity needed to maintain accuracy during machining processes, ensuring that parts are produced with consistent precision. Their low weight also reduces wear and tear on the machine, extending its operational life.
2. Vibration Damping and Stability
In many industrial applications, minimizing vibrations is essential for maintaining the accuracy and longevity of equipment. Carbon fiber tubes are highly effective at damping vibrations due to their stiffness and the nature of the material. This property makes them ideal for use in equipment where stability and precision are required.
A. Tripods and Mounting Systems
Carbon fiber tubes are increasingly used in the production of tripods and mounting systems for industrial equipment. Whether in surveying instruments, cameras, or measuring devices, the stability provided by carbon fiber ensures accurate readings and reduces the likelihood of errors caused by vibrations.
B. High-Precision Measuring Instruments
In industries where precise measurements are crucial, such as aerospace or automotive manufacturing, carbon fiber tubes are employed in the construction of high-precision measuring instruments. The material’s ability to maintain stability under various conditions ensures consistent and reliable measurements.
3. Corrosion Resistance and Durability
Industrial environments can be harsh, with exposure to chemicals, moisture, and extreme temperatures. Carbon fiber tubes offer excellent corrosion resistance, making them ideal for use in environments where traditional materials like steel would corrode over time.
A. Chemical Processing Equipment
In chemical processing plants, where exposure to corrosive substances is common, carbon fiber tubes are used in the construction of equipment such as piping, supports, and tanks. The corrosion resistance of carbon fiber ensures the longevity of the equipment and reduces maintenance costs.
B. Marine and Offshore Equipment
For marine and offshore industries, where equipment is exposed to saltwater and harsh weather conditions, carbon fiber tubes provide a durable solution. They are used in the construction of masts, booms, and other structural components that require resistance to corrosion and the ability to withstand high loads.
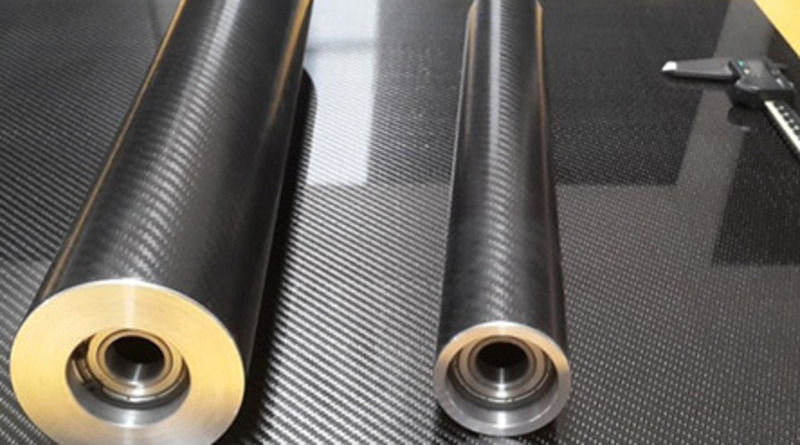
4. Customization and Flexibility
Carbon fiber tubes can be easily customized to meet the specific needs of various industrial applications. They can be machined, cut to size, and designed in various shapes and sizes to fit the requirements of different equipment.
A. Specialized Equipment Design
Industries that require specialized equipment, such as medical devices or aerospace components, benefit from the flexibility of carbon fiber tubes. Custom designs can be created to meet exact specifications, ensuring that the equipment functions optimally in its intended environment.
B. Additive Manufacturing and Prototyping
In the rapidly growing field of additive manufacturing (3D printing), carbon fiber tubes are used to create prototypes and small-batch production runs of industrial equipment components. Their ease of customization allows for quick iteration and testing, speeding up the development process.
5. Energy Efficiency and Sustainability
The use of carbon fiber tubes in industrial equipment contributes to energy efficiency and sustainability. The lightweight nature of carbon fiber reduces the energy required to operate machinery, and its durability ensures a longer lifespan for equipment, reducing the need for frequent replacements.
A. Wind Turbines and Renewable Energy Systems
In renewable energy systems, such as wind turbines, carbon fiber tubes are used in the construction of blades and structural components. Their light weight and strength allow for the production of larger and more efficient turbines, contributing to the generation of clean energy.
B. Electric Vehicles and Lightweight Machinery
In the push towards electrification and the development of lightweight machinery, carbon fiber tubes are used in the construction of electric vehicles (EVs) and other energy-efficient equipment. The reduced weight of these components leads to lower energy consumption and longer operating ranges for EVs.
Conclusion
Carbon fiber tubes have become an integral part of modern industrial equipment, offering unmatched strength, durability, and versatility. As industries continue to evolve and demand more efficient, reliable, and sustainable solutions, the role of carbon fiber in industrial equipment will only grow. Whether in automation, precision measurement, or renewable energy, carbon fiber tubes are driving innovation and enabling the development of next-generation industrial technologies.