1. When is Mechanical Processing of Carbon Fiber Tubes Needed?
Carbon fiber tubes are widely used in various industries, from aerospace to agriculture. However, in many applications, off-the-shelf carbon fiber tubes may not meet specific requirements. Mechanical processing is necessary when tubes need to be customized for particular uses. For example, in the agricultural drone industry, tubes may require precise drilling for attachments or threading for connections. Customization through CNC machining ensures that the tubes fit perfectly within the intended application, improving both functionality and durability.
2. Characteristics of Carbon Fiber Tube Processing
Mechanical processing of carbon fiber tubes can vary depending on the type of tube. Pultruded carbon fiber tubes, known for their high tensile strength, are generally easier to machine due to their straight fiber alignment. CNC machining can be used to cut, drill, or shape these tubes with precision.
On the other hand, wrapped carbon fiber tubes, which are made by winding fibers around a mandrel, present different challenges. The angled fiber layers can make machining more complex, requiring careful consideration of the machining angles and speeds to avoid delamination or fiber fraying. Understanding the specific properties of the carbon fiber tube being processed is crucial for achieving the desired results without compromising the integrity of the material.
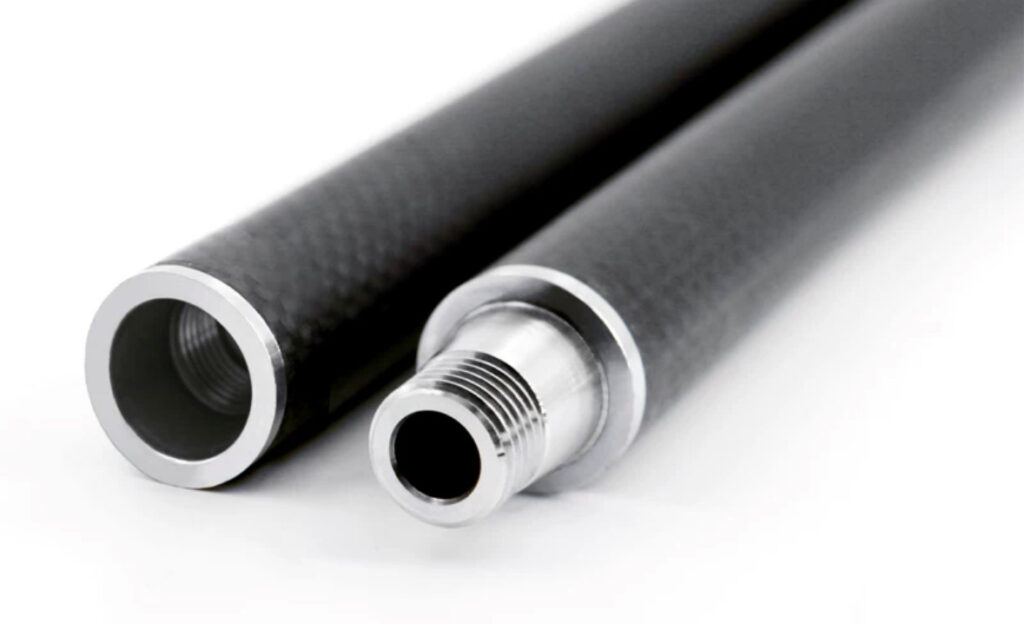
3. Choosing the Right Fittings for Carbon Fiber Tubes
Selecting the correct fittings for carbon fiber tubes is vital to ensure stability, strength, and aesthetic appeal. The choice of material for fittings, such as rubber, iron, or aluminum, depends on the specific application. Rubber fittings provide flexibility and shock absorption, making them ideal for applications where movement or vibration is expected.
Iron and aluminum fittings offer greater strength and are often used in more demanding applications. However, when using metal fittings, additional considerations must be made to prevent corrosion. Gold plating or anodizing are common treatments that protect the metal while enhancing the overall appearance. Ensuring that the fittings match the carbon fiber tube’s properties, such as thermal expansion and electrical conductivity, is essential for a secure and durable connection.
4. Installing Mechanically Processed Carbon Fiber Tubes
After mechanical processing, the installation of carbon fiber tubes must be done with care to maintain their structural integrity. Aligning the tubes accurately and using the right adhesives or fasteners is crucial. When joining multiple tubes, ensuring that the connections are tight and secure without exerting excessive force is vital to prevent damage.
For applications requiring high precision, such as in tripods or industrial equipment, the alignment and assembly process must be carefully monitored. Proper installation not only ensures the functionality of the tubes but also contributes to the overall aesthetics of the final product.
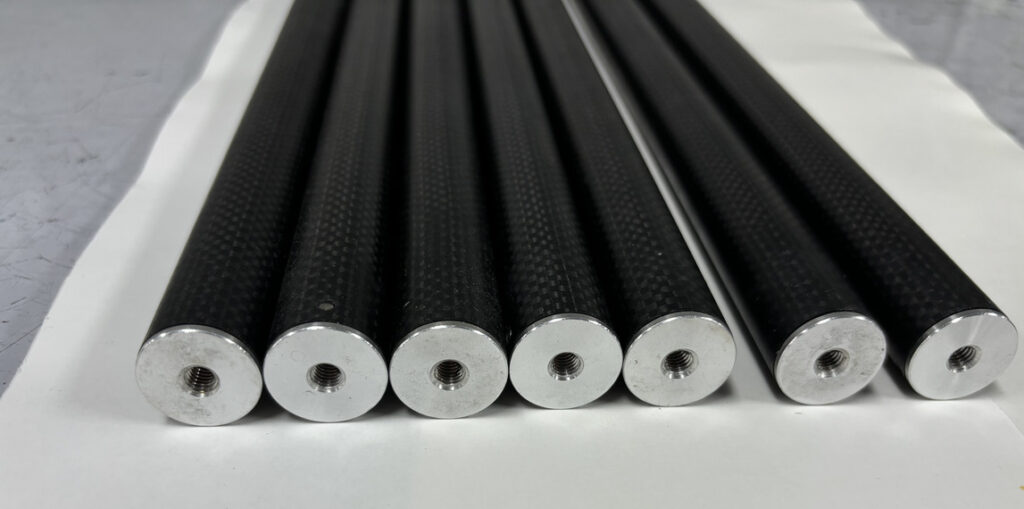
5. Conclusion
Mechanical processing of carbon fiber tubes is an essential step in customizing these versatile materials for specific applications. By understanding the characteristics of different types of carbon fiber tubes, carefully selecting the right fittings, and ensuring proper installation, the full potential of carbon fiber tubes can be realized. Whether for drones, tripods, or other industrial uses, precise machining and thoughtful assembly lead to superior performance and longevity.
https://www.rvmagnetics.com/overview-of-common-material-joining-methods-145